Your infant formula production line stops without warning. Spoilage claims are rising because of improper sealing. These are the nightmares that keep plant managers awake at night. The problem is that even small equipment issues can lead to huge losses in productivity and trust. This situation gets worse when you realize that every minute of downtime costs money and damages your brand's reputation, especially in a market where safety is everything.
To properly maintain canned infant formula packaging line equipment, you must create a comprehensive maintenance plan. This plan should combine proactive strategies like Total Productive Maintenance (TPM) and Reliability-Centered Maintenance (RCM). It also needs detailed, machine-specific checklists for daily, weekly, and monthly tasks. This approach ensures you follow strict hygiene standards, comply with regulations like those from the FDA, and keep detailed records for every piece of equipment, from mixers to labelers. Following these steps helps you build a clean, compliant, and productive plant.
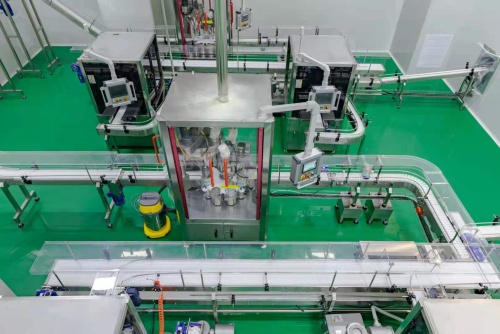
1. The Core Concept of Maintenance: Prevention First, Compliance Based
In the production of infant formula milk powder, we always prioritize food safety and quality. This means that our maintenance work is not only to extend equipment life or improve efficiency, but also to ensure that products are not contaminated throughout the entire production process and comply with the strictest regulatory standards.
Compliance: Compliance documents impose strict requirements on all aspects of infant formula production, so the primary principle we adhere to in carrying out maintenance work is compliance. For example, the FDA's Current Good Manufacturing Practices (CGMP) and Food Safety Modernization Act (FSMA) are the cornerstone for developing maintenance plans. These regulations require manufacturers to establish effective control measures covering all aspects of equipment design, operation, and cleanliness to prevent potential food safety issues. So producers need to regularly review and update maintenance procedures to ensure compliance with the latest regulatory requirements.
Preventive maintenance (PM): It is well known that "prevention is better than cure". By implementing a comprehensive preventive maintenance plan, potential issues can be identified and resolved before equipment failures occur, thereby avoiding costly downtime, reducing maintenance costs, and extending the lifespan of equipment. This includes regular inspections, cleaning, lubrication, and component replacement.
Reliability, Availability and Maintainability (RAM) Analysis: The RAM analysis is employed to evaluate the overall performance of the production line. By analyzing the reliability (the probability of the equipment performing the required function under specific conditions), availability (the proportion of time the equipment is available for production), and maintainability (the ease with which the equipment can be quickly repaired in case of failure), the weak links in the production line can be quickly identified, and maintenance strategies can be optimized to maximize production efficiency and profitability.
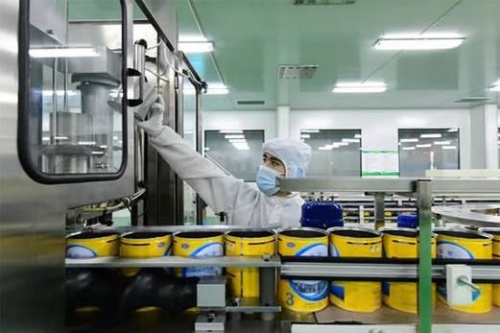
2. Key Maintenance Points for Critical Equipment
The canned milk powder packaging line involves a variety of key equipment, and each piece of equipment has its own specific maintenance requirements. Here are some maintenance practices we have adopted for the main types of equipment:
2.1 Mixers
Mixing is the first step in the production of infant formula milk powder, and its quality directly affects the uniformity and stability of the final product.Daily inspection and cleaning: After each production cycle, thoroughly clean the mixer to prevent product residue from accumulating. This is crucial for preventing cross-contamination and maintaining product quality. At the same time, ensure the use of cleaning agents suitable for the equipment materials (such as stainless steel).
Lubrication: Follow the manufacturer's recommendations to regularly lubricate moving parts such as bearings, gearboxes, belts, and seals to reduce friction and wear.
Component inspection and replacement: Regularly inspect the wear of mixing blades, paddles, belts, and seals. Once signs of wear are detected, replace them immediately to prevent minor issues from escalating into major failures.
Calibration: Regularly calibrate temperature sensors and safety control devices to ensure their accuracy.
2.2 Homogenizers
Homogenizer is used to ensure the uniformity and stability of formula milk powder, especially in the production of liquid formula milk powder.Daily inspection: Check the oil level every day and add it when necessary.
Regular cleaning and lubrication: The pistons, cylinders, valves and seals of the homogenizer need to be cleaned and lubricated regularly. Replace worn parts, such as seals and valves, periodically.
Performance monitoring: Use techniques like vibration analysis, thermal imaging and oil analysis to monitor the performance data of the homogenizer, so as to intervene before potential problems escalate into serious failures.
Manufacturer's recommendation: Strictly follow the maintenance frequency and guidelines in the original equipment manufacturer's (OEM) manual.
2.3 Dryers
In the production of powdered infant formula, drying is a key step, and a drum dryer is usually used to convert the liquid mixture into powder.Daily cleaning: Clean the exhaust port system, lint filter and drum of the dryer every day to ensure optimal performance and prevent blockages.
Regular inspection: Regularly inspect the drum belt and rollers to ensure their normal operation.
Record and documentation: Keep detailed records of the performance data of the dryer, maintenance activities and any abnormal situations. These records are crucial for troubleshooting, compliance verification and the optimization of future maintenance plans.
2.4 Filling Machines
The filling machine is responsible for accurately filling milk powder into containers, which is the key to ensuring product weight and packaging integrity.Daily cleaning: After each production cycle, the filling machine, especially the nozzle and pipeline, should be thoroughly cleaned to prevent product residue accumulation and cross contamination.
Lubrication: Regularly lubricate moving parts such as bearings, chains, and seals, and ensure the use of the lubricant type recommended by the manufacturer.
Visual inspection: Conduct a quick visual inspection every day to look for loose bolts, worn belts, or broken components, so as to detect and solve problems early.
Safety system inspection: Regularly check safety functions such as emergency stop buttons and protection sensors to ensure their normal operation.
Replacement of worn components: Worn components such as seals, belts, and nozzles will be replaced regularly (usually every 6 to 12 months) depending on usage.
Sensor calibration: Liquid level, volume, or pressure sensors need to be calibrated regularly to ensure filling accuracy, which is particularly important in the food and pharmaceutical industries.
Troubleshooting: Train operators to identify and solve common problems, such as product leakage (usually caused by worn seals or loose connections), nozzle blockage (solved through daily cleaning and using dedicated nozzles), and belt wear (resolved by checking tension and replacing promptly).
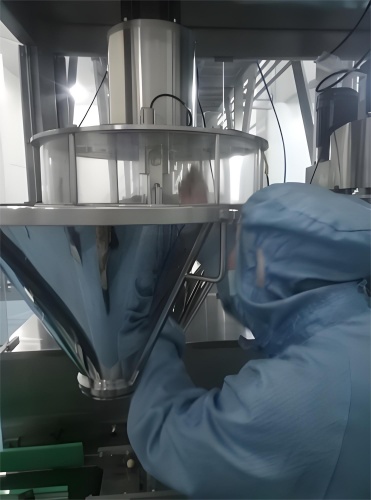
2.5 Sealing Machines
The sealing machine ensures the sealing integrity of the containers, which is crucial for the shelf life of the products and the prevention of contamination. Vacuum powder filling (VPF) is the "gold standard" for filling infant formula milk powder. It is filled in a vacuum environment, reducing the contact between the product and air, and eliminating the moving parts in contact with the product, thereby improving hygiene levels and product integrity.Daily inspection: Check the cleanliness of the sealing lever, cutting knife and chopping board every day, and remove any debris or packaging materials to prevent blockages.
Weekly maintenance: Lubricate the moving parts (such as the sealing clamp) with food-grade lubricant weekly, and clean the exterior of the machine with a mild cleaner. Check the electrical connections and wires, and verify the accuracy of temperature and pressure settings.
Monthly maintenance: Conduct a more in-depth inspection monthly, especially for wear-prone components such as the sealing head, rollers and bearings. Check if the bolts are loose, if there are any misalignments or other mechanical issues.
Hygiene design: Choose a sealing machine with excellent hygiene design to prevent powder spillage, and use the feeding screw instead of the feeding chain to avoid lubricant exposure, thereby minimizing the risk of product contamination.
2.6 Labeling Machines
The labeling machine is responsible for accurately attaching labels to the products, and it is an important part of product identification and brand image.Daily cleaning: Clean all sensors and rollers every day, remove any label debris, and check for loose screws and fasteners.
Weekly maintenance: Lubricate moving parts weekly, inspect the wear of the rollers, and test the synchronization with the automatic filling machine.
Monthly tasks: Replace worn belts or sensors monthly, check if the entire system is corroded or mechanically damaged, and run calibration and test label accuracy.
Software and firmware updates: Regularly update the software and firmware of the labeling machine to fix errors, improve functions, and introduce new features.
Calibration Check: Regularly calibrate the label sensor to maintain the accuracy of label detection. Incorrect calibration may result in label skipping or duplication.
Troubleshooting: Train operators to solve common problems, such as label misalignment or wrinkling (by adjusting the label applicator position and checking the label tension) , label blockage (by checking the label path and roller condition), and inconsistent label application (by evaluating the label application speed and checking the label placement sensor).
3. Best Practices and Management Strategies for Maintenance and Upkeep
In addition to the specific maintenance points for certain devices, a series of overall management strategies should also be implemented to ensure the effectiveness of the maintenance work and continuous improvement.
Operator Training: Provide comprehensive training to all equipment operators to enable them to identify and solve daily maintenance issues, and perform basic troubleshooting tasks. Well-trained operators form the first line of defense in preventive maintenance.
Documents and Records: Keep detailed records of all maintenance tasks, component replacements, and troubleshooting activities. These records can help track the equipment history, identify recurring problem patterns, and provide data support for future maintenance plans.
Spare parts inventory management: Maintain on-site inventory of critical spare parts, including commonly used components such as rollers, sensors, and belts. Ensure quick replacement in case of unexpected issues, minimizing downtime to the greatest extent possible.
Follow manufacturer's guidelines: Strictly adhere to the manufacturer's instructions for all equipment, including maintenance frequency, lubricant type, and operating parameters.
Regular Audit and Inspection: Conduct regular audits of maintenance processes, including label application quality, machine settings, and overall system integrity. Any exceptions will be dealt with immediately.
Environmental Control: Strive to maintain a controlled environment conducive to equipment operation, including temperature, humidity, and cleanliness.
Continuous Improvement: Establish a feedback mechanism to encourage operators to propose improvement suggestions. These continuous improvement measures help enhance equipment efficiency and reliability.
Total Productive Maintenance (TPM): Promote the TPM concept, which is an innovative approach that extends equipment maintenance responsibilities to the production team. TPM aims to maximize equipment overall efficiency (OEE), reduce downtime, and improve product quality through eight pillars such as self-maintenance, planned maintenance, and quality maintenance.
By implementing these comprehensive maintenance and upkeep strategies, not only can the packaging line for canned infant formula be ensured to operate continuously and efficiently, but more importantly, it also guarantees the highest quality and safety of infant formula, providing reliable products for infants worldwide.
Union Machinery has been engaged in food machinery customization services since its establishment in 2014, according to customer needs for you to tailor suitable machinery and equipment, for more product information, please refer to: Milk Powder Filling Production Line;Our expertise and advantages will bring you more opportunities and development space.
For personalized, industry-tailored advice and to explore state-of-the-art solutions, please don't hesitate to contact us at info@unmachinery.com
The following is other knowledge related to milk powder packaging line that I have summarized based on long-term work experience, for your reference. I hope it will be helpful to you.
1.How to Build an Efficient Canned Milk Powder Packaging Line?
2.How to Select the Right Infant Formula Packaging Equipment for Global Markets?
3.What Are Common Problems with Powder Filling Machines and How to Fix Them?
4.What Are the Common Types of Infant Formula Packaging Machines?
5.How to best analyze the price and cost-effectiveness of milk powder canning equipment?
6.How Can You Master Dust Control During Infant Formula Canning?